Defect Management Steps and Strategies
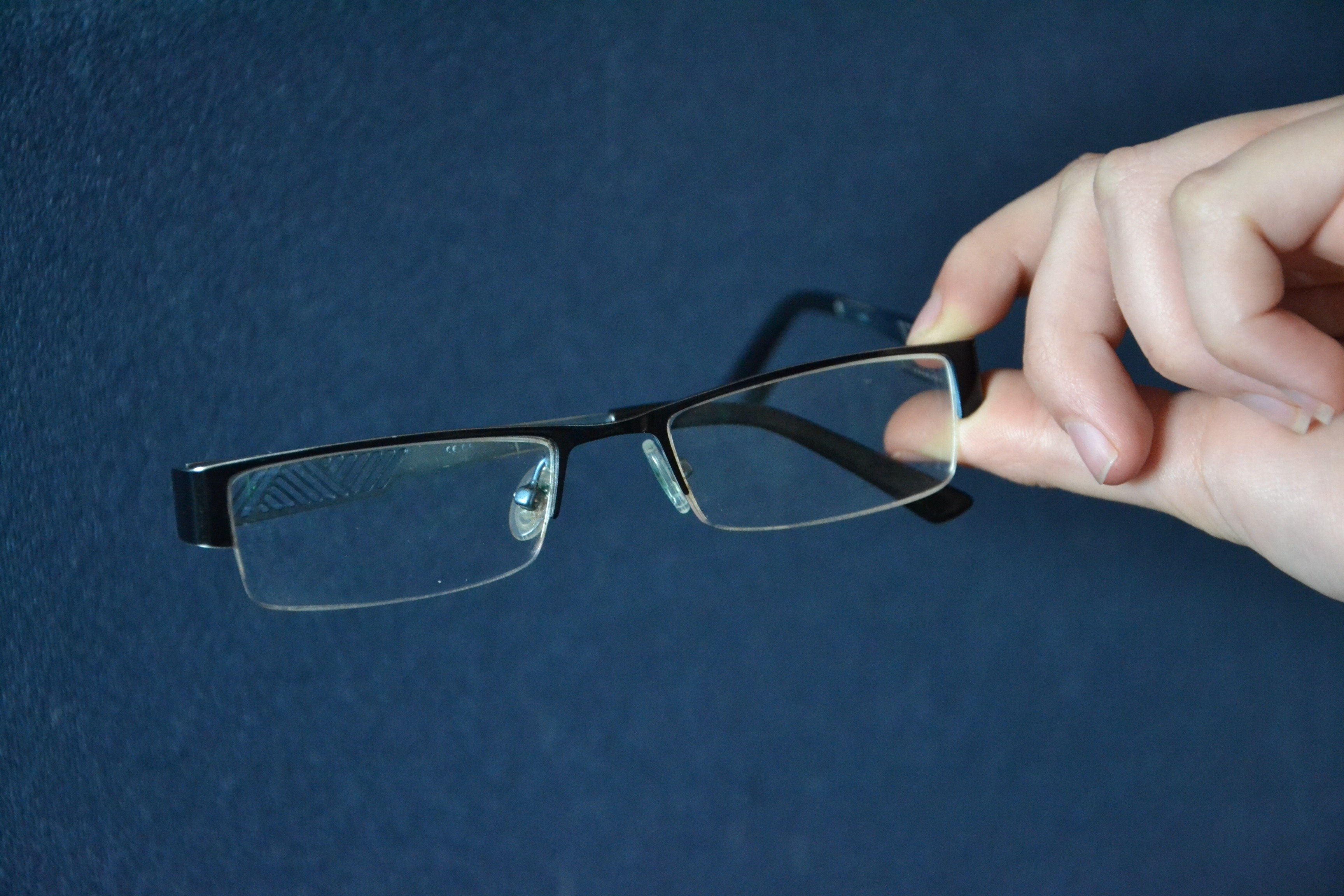
- Date: 01 Feb, 2021
In a software development process, the best defect is the one that never occurs. In the real world, prevention is better than a cure. However, to reach this state of perfection in a product development process, tool or team, it is important to ascertain how to manage defects to continuously improve products. The problem is that defect management is often considered a small piece in the development process that belongs to one or two teams in the companies with no need for improvement. But this problem can be overcome by using the right steps and the right strategies for making the process more effective and efficient.
Defect Management Stages and Strategies
Following are four steps to assess your state with respect to defect management, identify the possible gaps, and move closer to achieving defect-free software:
-
Defect Visibility
As a team leads or QA manager, it is important to ascertain if your team has visibility into the defects discovered across different products and teams. It is true to say that we cannot manage what we cannot see. A team can only develop a new product by managing the fluctuating variables of cost, quality, features, and time. Without visibility into defects of a product, it is difficult for a team to know what decisions are made and how they will impact other efforts to complete a product. Visibility starts with understanding and accepting the process of defect management and by using defect management tools. This could be simply by using spreadsheets for small businesses to an organization with a complete database built with defect management practices at hand.
-
Defect Prioritization
Is there a way to perform risk analysis and prioritization of defects? After the first step of visibility, a QA manager needs to ensure that the team is tracking the right defect data, and so the information that matters can lead to action. Data for the sake of data is noise. In order to ensure active team participation, it is important to ensure the quality of data. Teams need to prioritize the defects by capturing the right information to take action today and prevent defects in the future. Thus, they need to consider the quality, accuracy, and purpose of the data.
-
Defect Resolution
As a QA manager, you need to check if you have a timely way of acting on defect information. With visibility and the right quality data, teams have more opportunities. They can make timely decisions faster and earlier in the process. Studies show the costs of fixing issues later rather than earlier in the process are higher. Thus, collaboration, assignment tracking, and proper closure are important for action. Defect management tools should be capable to ensure the resolution becomes a part of the quality data captured, not just happening in the emails. A better tool will help your team increase participation with friendly features such as chat interfaces, email notifications, and easy filtering to point out the defects that are important. So a process and system should provide fast, team collaborative steps to resolve defects with the capture of discussions and resolutions.
Defect Analysis
A QA team should have a defect prevention process and culture to drive minimum defects. Once a team has the visibility, prioritization, and resolution of defects working well, QA teams can consider the defect analysis and review process, which considers both inputs about individual defects by classifications, product lines, revision history, involved teams, and much more. Defect analysis moves teams closer to ensure zero defects in their products.
Conclusion
Although it is hard to take the time to review a process once it is complete. Yet it is a discipline found in most growing companies, so we insist that you consider the above-mentioned steps and strategies in a software development process to ensure software quality. These steps can be followed by using defect management tools. QA engineers divert and reassign idle resources frequently and not the results desired. It is recommended to use some of the team’s idle time to assess the defect management process and drive to that zero defects goal. Make sure that you consider the risks of driving defect management as a priority for the company. Or what does your business have to lose in making it a priority? Well, there is nothing much that you would lose but can gain faster release cycles, better cost controls, reduced risks, happy customers, and brand integrity. Is that too much to ask for? Fortunately, that is all possible with the right defect management tools.
- Tagged in: defect management QA